,cnc machinist,cnc manufacturing,cnc mechanic,cnc mill,cnc milling center,cnc milling companies,cnc milling tools,cnc parts,cnc plasma cutter,cnc plasma cutting,cnc plasma table,cnc production,cnc router table,cnc screw machine,cnc service,cnc swiss,cnc turning,cnc turning center,cnc turning centers,cnc vertical lathe,horizontal cnc,how to cnc machine,machining cnc,manufacturing cnc machines,okuma cnc,plasma cnc machine,production cnc machining,troubleshooting cnc machines,used cnc machine tools,used cnc milling machines,vertical cnc lathe,what can a cnc machine make
Threading:-
Out of different fastening process threading is one. This process is widely used because it doesn’t join two parts permanently giving the flexibility of disassembling them when needed
What is a Thread?
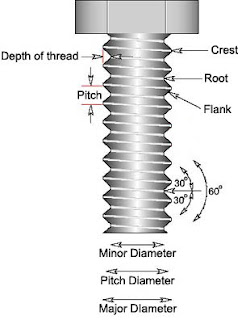
Application:-
Thread is one of the most used processes in mechanical field. In everyday life we come across through many type of components that have a thread in it. Take example of a pen cap or a water bottle etc.
Understanding a thread:
v The crest is the peak or top of the thread ridge that lies between two flanks. Its size and shape may vary depending on the thread type.
v The flank is an angled side of a thread. Threads have two flanks.
v The root is the bottom of the thread that lies between the flanks. Its size and shape also may vary depending on the thread type.
Type of thread:-
Depending on Geometry thread is classified into two categories. A) Straight threads B) taper thread.
Straight threads can be classified into single start or multi start threads.
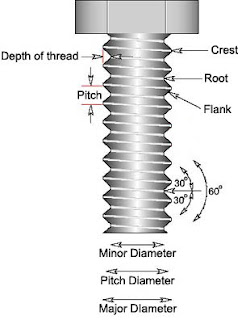
Important parameters on the thread:-
- v The pitch point is the position on the thread where the distance between the flanks is equal in both the ridge and the groove.
- v The pitch diameter is the measured distance between the pitch points in the groove between the threads. It is one of the most important dimensions in thread inspection.
- v The depth is the length of the vertical space from the root to the crest of a thread.
- v The major diameter is the distance between the crests of a thread. It is the widest diameter on a thread.
- v The minor diameter is the distance between the roots of a thread. It is the smallest diameter on a thread.
- v Thread form which is the shape of the thread example 90 degree, 60 degree threads etc.
Start, Pitch, and Lead
Start:-
Start refers to the number of different individual threads that wrap around the cylinder. The number of threads equals the number of starts. It means how many start points are there in a thread.
Pitch:-
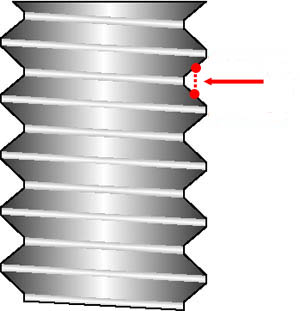
Lead:-
Lead is the distance that a screw travels in one revolution. This distance is equal to the pitch of the screw multiplied by the number of starts on the screw. On a single-thread screw, the lead equals the pitch.
Threads can be manufactured in one of the below mentioned process.
- v Thread cutting and thread milling are cutting methods that use a single-point tool and multi-point tool, respectively, to create threads on a blank or work piece.
- v Thread rolling is a cold forming process that uses a die to deform metal and press it into the shape of threads. Figure 2 shows the mechanism that holds the dies.
- v Thread tapping uses a drill-like tool to either cut or form threads on the ID of a previously drilled hole.
- v Thread grinding uses an abrasive wheel to wear away material and create the thread. Thread grinding is the most precise method of producing threads
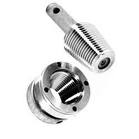
A lathe uses a single-point tool, to cut the threads into the blank or work piece, which is held either between centers or in a chuck. The cutting tool is fed into the blank and moved sideways along the rotating piece. On the first pass, the tool is often used to scratch the surface so that the operator can inspect the scratch and verify the tool settings. Then the tool makes multiple passes, cutting deeper each time the tool travels the length of the cylinder.
Milling is another form of cutting. Thread milling is performed similarly to lathe cutting except that a multi-point tool is used. Also, when using a mill, it is usually the tool, not the work piece, that rotates. Milling can be performed more quickly than other methods, but it is generally not recommended for manufacturing smaller threads.
To continue ……………